Lake Bonney Expedition 2008
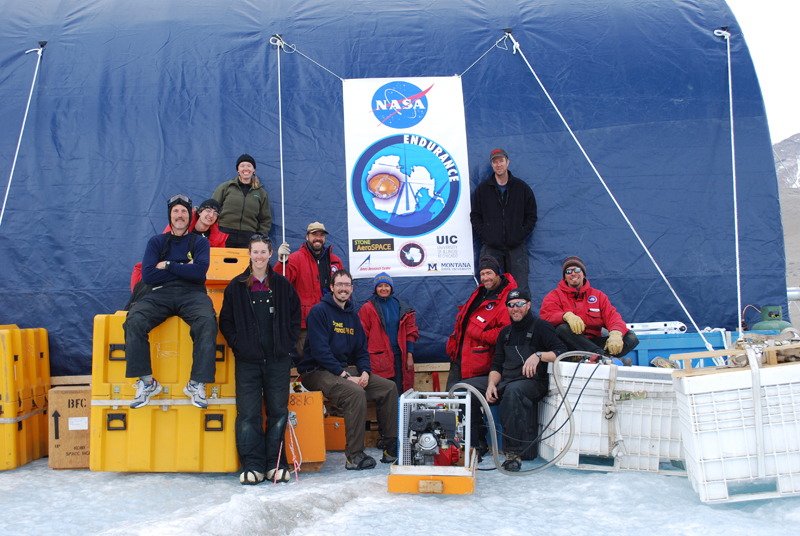
The first deployment is under way.
Here are the second week's blog entries from Vickie Siegel.
For the most recent entries see the bonney 08
blog
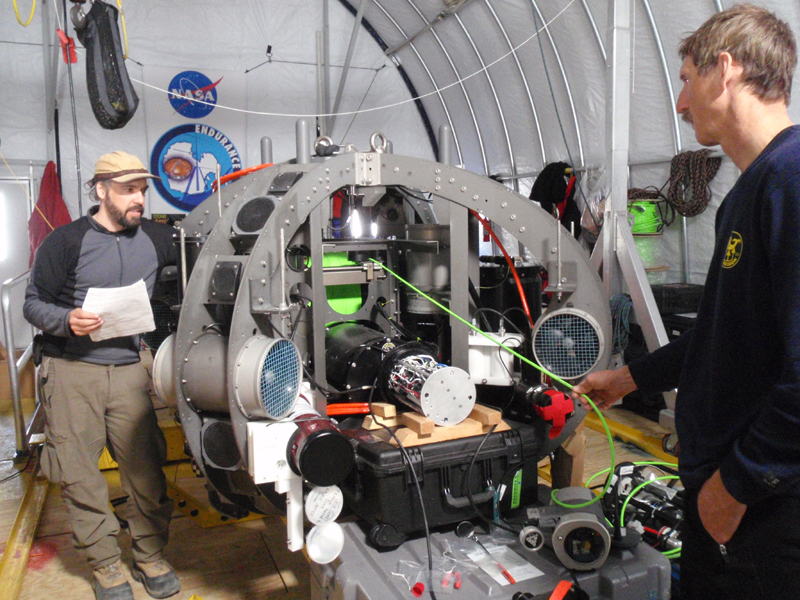
Bart and Bill test that the profiler is spooling cable in and out properly. The open profiler electronics pod is sitting on wood blocks between them
Tuesday
December 9, 2008
Thanks to Bart’s long night with the servo driver
electronics, we were ready to test the fix this morning. We
hooked the pod, with electronics still exposed, to the bot and ran some
tests in air to see if everything was functioning normally. Once
we saw that the profiler drum was spooling out and winding up as
directed we sealed the housing back up and spent a few hours remounting
it into the bot. Now it was time for the real test—putting it
back in the water. We lowered the bot nervously. Every time
we open an electronics housing we run the risk of scratching the pod’s
sealing surface or pinching an o-ring. Either mistake will allow
the pod to leak, an obvious catastrophe. We were relieved,
therefore, when the leak detector board in the pod showed normal data,
no leaks. Even better was the news that the profiler was working,
even after it had cooled down. We weren’t getting any temperature
faults. Another hurdle is out of the way.
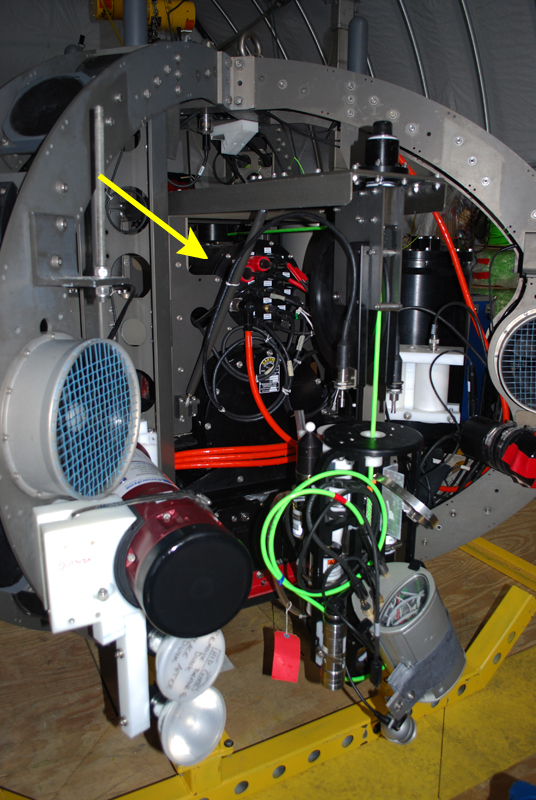
Here is the pod we have to remove, right in the center of the vehicle
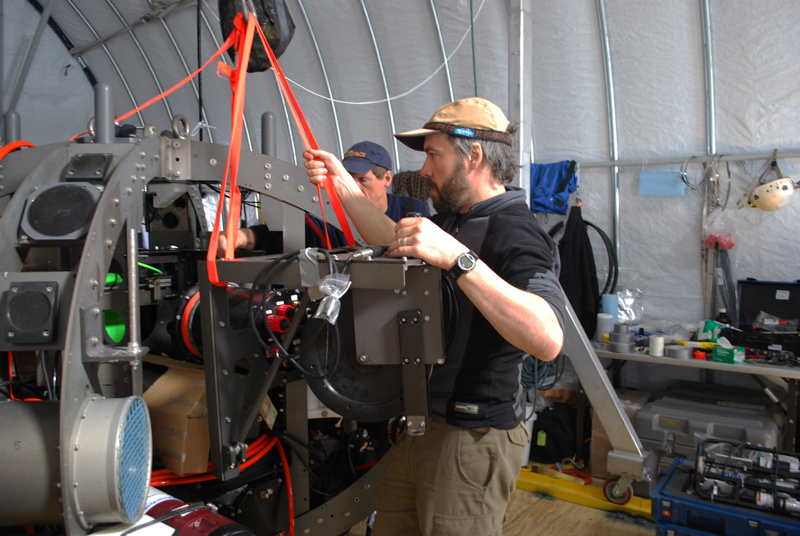
Bart slowly slides the electronics pod and pulley assembly out of the vehicle
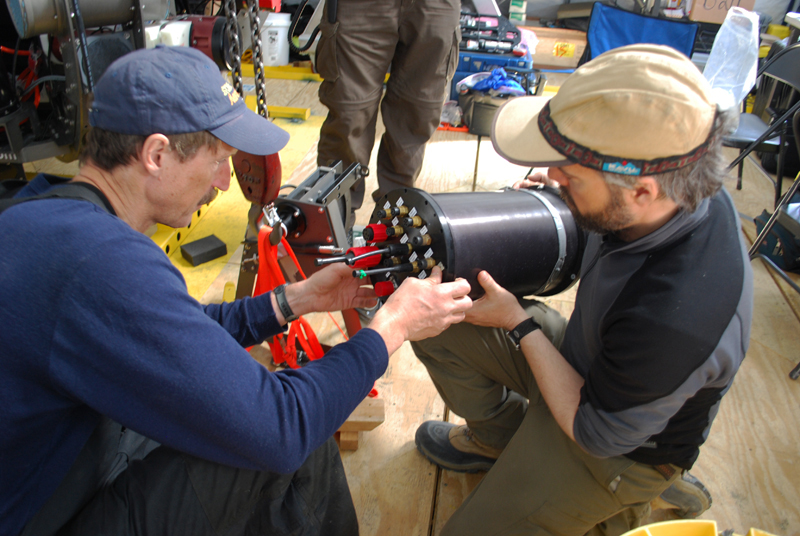
Bill and Bart inspect the pod after we’ve detached the pulley assembly
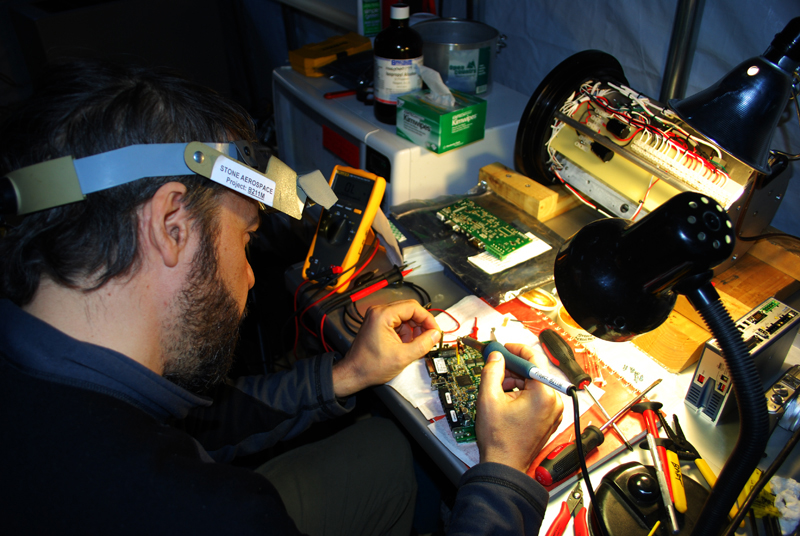
Bart works late into the night opening up the pod, digging through the layers of electronics and soldering in the resistors
Monday
December 8, 2008
With yesterday’s success and some navigation data
for the programmers to occupy themselves with, today seemed like a good
day to work on the problem with the profiler. Through some
research, Bart had established a few things. For one, the
driver’s manual claimed that at the worst case limits, the driver would
still give full performance at 0ºC, even though ours had failed at
10ºC. 0ºC is colder than the temperature the driver
will be operating at in Bonney, so the driver should have worked.
Second, it turns out that the manufacturer had improperly set the low
temperature limit, an oversight they apologized for and will repair in
all future units. Third, the temperature fault was being
triggered by a thermistor in the servo driver electronics. There
are several ways to get around this problem and all of them involved
getting into the driver’s electronics. What Bart decided to do
was to spoof the electronics by adding a fixed value resistor.
The first step of this repair was to remove the housing that contains
the profiler electronics. Unfortunately, this is not easy.
Of all of the housings we might need to open, the profiler electronics
pod is in the physical heart of bot, buried in cables, metal frames,
pulleys and so on. We had to remove the drop sonde from its
cable, remove the pulley, and undo dozens of nearly-impossible-to-reach
bolts. To everyone’s surprise, we had the pod out in only two
hours.
Pulling the pod out of the bot was only the beginning of the
process. Once we had opened the pod, it took Bart several more
hours to meticulously remove the electronic components that blocked his
access to the servo driver electronics, where he needed to work.
He decided that the easiest fix to our temperature fault problem was to
spoof the firmware temperature fault control so that it would never
trip off. He did this by soldering a standard value resistor in
parallel to the thermistor that had been built into the driver by the
manufacturer. A thermistor is a like a temperature sensitive
resistor. At lower temperature it provides less resistance and at
higher temperature it provides more resistance. Placing another
resistor in parallel to the thermistor adds to the total resistance
“felt” in that part of the circuit. Since the firmware equates
higher resistance to higher temperature, it is fooled by this new high
resistance to think that the temperature is higher than it really is
and it doesn’t trip the fault.
Its good in theory and we all hope its going to work.
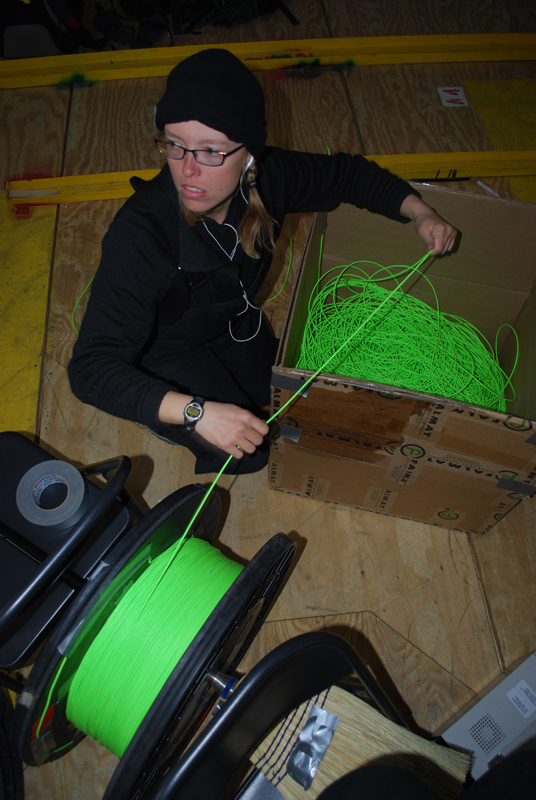
Vickie unspools the kilometer-long fiber optic in preparation for the bot’s 380 meter journey away from the melt hole today
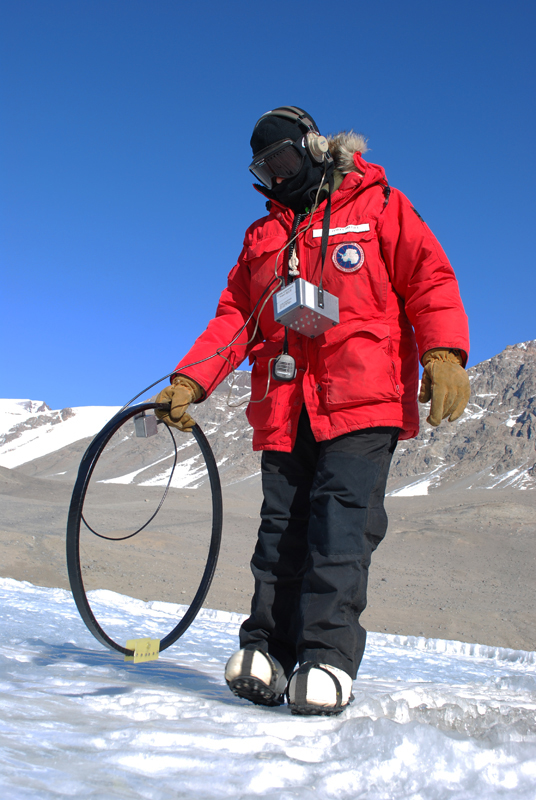
Vickie tracks the bot’s magnetic beacon using a loop antenna
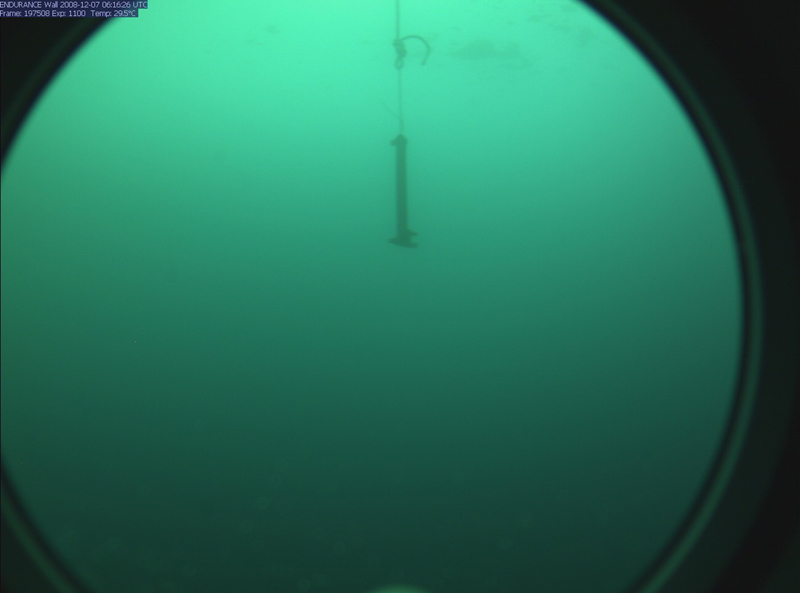
This image comes from the bot’s forward looking camera. When we saw the wrench in the field of view, we knew that we had reached the flagged point on the surface successfully
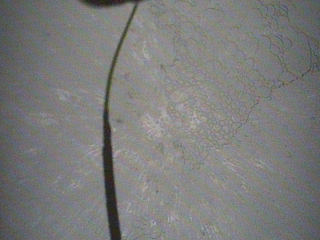
The bot moves along under the ice, the string is wiggling above the camera is the fiber optic line. It reaches the edge of the melt hole, it identifies the blinking light, locks onto it and ascends to a cheering crowd
Sunday
December 7, 2008
Today we decided to spread our wings a little bit and try a longer
run. We had two goals to start with. The first was to make
sure the navigation really is rock solid even over long distances and
the second was to try and find another piece of lost equipment that
Peter thought might be waiting to snag us. These goals would take
the bot 380 meters from the melt hole, which is actually the farthest
we’ve ever sent the bot away from mission control, even including all
of our previous tests in the states and the DepthX missions in
Zacatón. In preparation for this rite of robot passage,
Vickie swapped out the 400 meter long fiber optic line we had been
using up to now for a 1000 m line. While normal fiber optic would
sink and droop down to the halocline in Lake Bonney, this fiber optic
has a special coating that allows it to float up to the ice
ceiling. This way, when the bot spins in a circle or lowers the
sonde, it won’t get wrapped up in the fiber.
A destination point was entered into the bot’s navigation system and
Endurance motored off while Peter, Bill, and Vickie tracked it from the
surface. The target was the last known GPS location of an old
ablation stake (essentially an ~8 meter long rod used to measure how
much the lake ice ablates over time) that had disappeared into the ice
in a previous year. Peter said there was a small chance that the
stake could be sticking straight up out of the lake sediment and might
serve as a fiber optic snag if we didn’t check it out first.
The GPS point we had turned out to be inaccurate by several meters but
there was also a flag marking the spot on the surface so, since we were
able to locate the bot from its magnetic beacon, Bill was able to
report a heading and distance to Shilpa, Kristof, and Chris at mission
control and they were able to drive right to the spot, confirming that
both navigation and beacon were working correctly. A wrench
securely tied to some rope had been lowered down a small melt hole at
the target so that, looking from the forward-looking camera, mission
control would be able to confirm that they reached the spot.
Reach it we did and we proceeded to investigate the area, spinning the
vehicle and using the forward-cam to look for the missing ablation
stake. After some time spent hunting for the stake we decided to
bring the bot home for the final test of the day: visual homing.
One of the interesting technological problems with working under a 3
meter ice cap is the question of how to get a 2 m x 2 m bot covered
with delicate instruments back out of the melt hole you tossed it
into. Coming from the DepthX project, we knew that the bot’s
dead-reckoning navigation was quite good and could get us back to
within a few meters of the melt hole. But short of manually
driving the vehicle up the 3 meter tall melt hole, how could we get it
to ascend at the right time? The answer was machine vision.
We have an upward looking camera on the bot and above the center of the
melt hole we have a 12 watt LED light that blinks on and off on a
specific frequency. Shilpa worked with Aniket and Greg, two Stone
Aerospace programmers back in Austin, to write a visual homing program
that would start up when the bot approached the melt hole. It
would use the camera to identify all of the light sources above it,
pick out the bright light that blinked at the right frequency, lock
onto that light, and then kick in the appropriate thrusters to center
the vehicle under the light and follow it up to the surface. That
is, if it worked.
We had tested the visual homing in our final bot tests over the summer
and it appeared to work well in the wide open waters of NBL’s
brobdingnagian tank. However, we had never been able to test how
it would perform in a tall, narrow tube like the melt hole, where the
consequences of running just a little off course meant hitting the
wall. Shilpa urged us all to have faith in the program as we
leaned over the railings around the melt hole, looking down and waiting
for the bot. The orange edge of the bot’s syntactic became
visible in the southwest quadrant of the melt hole. It started to
pass under the hole, still under normal navigation. The regular
pulse of the blinking light flashed off the water surface onto our
faces. As the bot passed under the hole it stopped, shimmied a
little to one side and then to the other, centering itself before
ascending gracefully up the hole. The skin of the syntactic broke
the surface of the water and the whole room cheered. Not only had
the bot navigated to a target 380 meters away under a 3 meter ice cap,
but it came home and, using the visual homing, popped straight up to
the surface like all good robots should. We are beginning to feel
like all of our hard work is paying off.
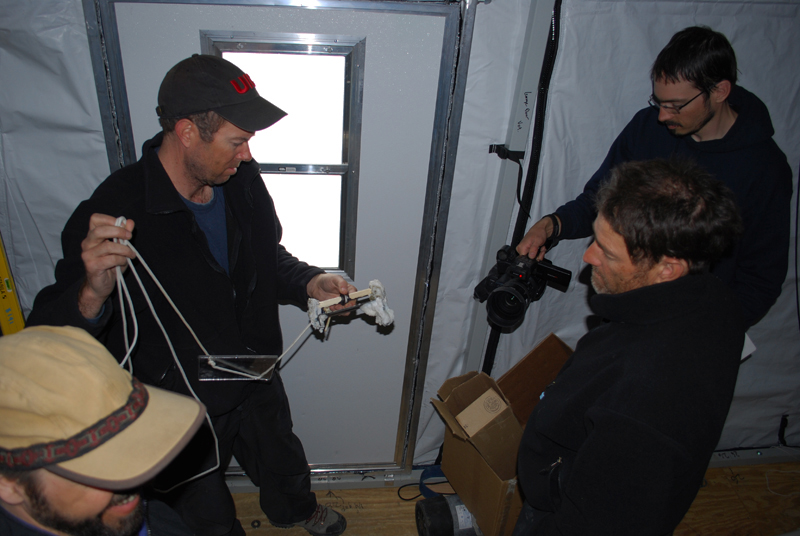
Peter displays the mystery experiment pulled out of the lake. The white goop on the body of the thing is salt from the lake. We salvaged the square of Plexiglas for use as a prototyping material later - you never know what you’ll need in the field
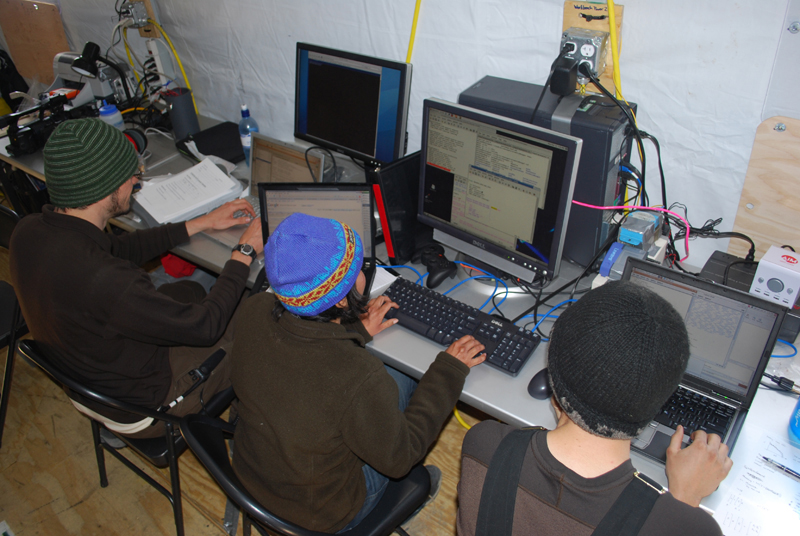
Kristof, Shilpa, and Chris track the bot’s progress from mission control
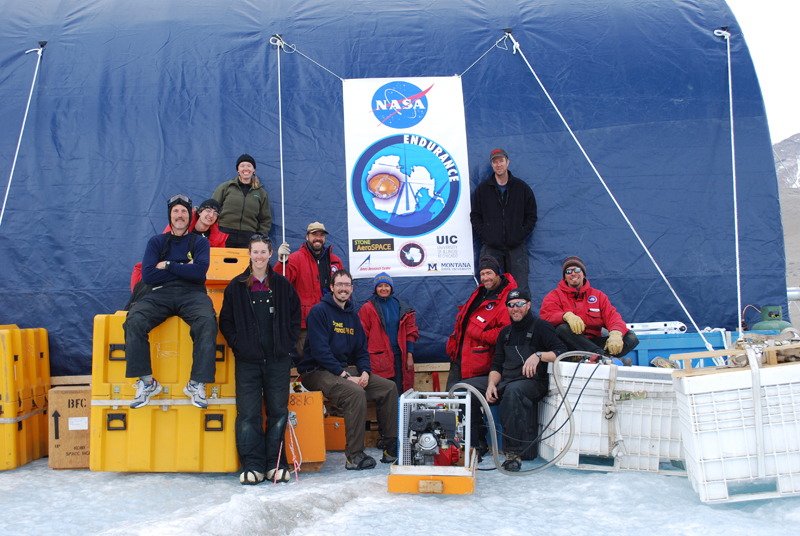
One last shot of the team before Bob and Annika leave. From left to right: Bill, Chris, Vickie, Annika, Bart, Kristof, Shilpa, John, Peter (standing in back), Bob, and Maciek
Saturday
December 6, 2008
At breakfast today, Peter announced that he and
John had
decided
that we would not switch to our second melt hole further down the lake
as we had originally planned. Our time this year is better spent
collecting more data here near the glacier and running the sonde drops
we’ve planned for this side of the lake than to spend the 4 days it
would have taken to break down the Bot House and move it to the other
end of the lake and set up shop all over again.
We decided to proceed with more non-profiler tests today while Bart
continues his dialog with the servo driver tech support. Today is
Friday in the states so it his last chance before the weekend to talk
to them before we attempt a solution.
Today’s testing schedule included doing some ground truthing of the
navigation programs and to test our recovery beacon. Happily, it
was easy to both at the same time, since we could use the recovery
beacon to locate the bot and verify if it actually navigated to the
points it was programmed to go to. We sent the bot down
under the ice and gave it some coordinates to drive to about 10 meters
away from the Bot House. Bill and Vickie, meanwhile, suited up
and went out side with the loop antennas.
Our recovery beacon is a meter-long cylinder that hangs inside the bot
frame and produces a magnetic field. The field can be sensed
above the ice by a loop antenna, essentially a coil of wire about a
half meter in diameter. The loop antenna plugs into a receiver
box and the receiver box has a set of headphones. The operator
wears the headphones and can hear the signal. When the signal
goes null, or makes no noise, then the loop is pointed directly at the
robot. When there is a loud tone then the loop is pointed away
from the bot. With two people using loop antennas, it is a simple
matter to zero in on the beacon.
When mission control radioed that the bot had reached its waypoint and
stopped, Vickie and Bill located the bot and marked the spot with an
ice screw. A GPS check confirmed that the bot appeared to be
navigating correctly. Good news!
The next thing Peter wanted to check on was a mystery object stuck in
the lake. Several researchers have worked in Lake Bonney over the
years and occasionally the equipment from their various
experiments — ropes, sediment traps, stakes, etc--is lost or forgotten
in
the lake ice. One of our biggest fears is that Endurance will run
into one of these objects dangling below the bottom surface of the ice
and get the fiber optic snared. When we chose the site for our
Bot House, Maciek found some crossed bamboo stakes lying on the ice
nearby. It turned out that there was a string tied to them and
some sort of object, one of these old experiments, dangling from the
string in the water. We navigated to where we calculated the
bamboo stakes to be and, approaching carefully, looked at this mystery
obstacle through the forward looking camera. We could see some
sort of dumbbell - shaped object but couldn’t tell what it was.
Maciek then melted the object out of the ice. When Peter returned
to the Bot House carrying the retrieved object we all crowded
around. It was much smaller than it looked on the screen and no
one had any idea what it was, just that it was corroded and crusted
with salt that had precipitated onto it from the salty lake.
While it remains a mystery, we’re just happy to have this obstacle
removed from our path.
While today went well, the end of the day was still a bit of a
bummer. Bob and Annika left on a helo flight this afternoon and
after a day or two in MacTown they’ll be heading off to holidays in New
Zealand. Thanks for your help guys, we’ll miss you!
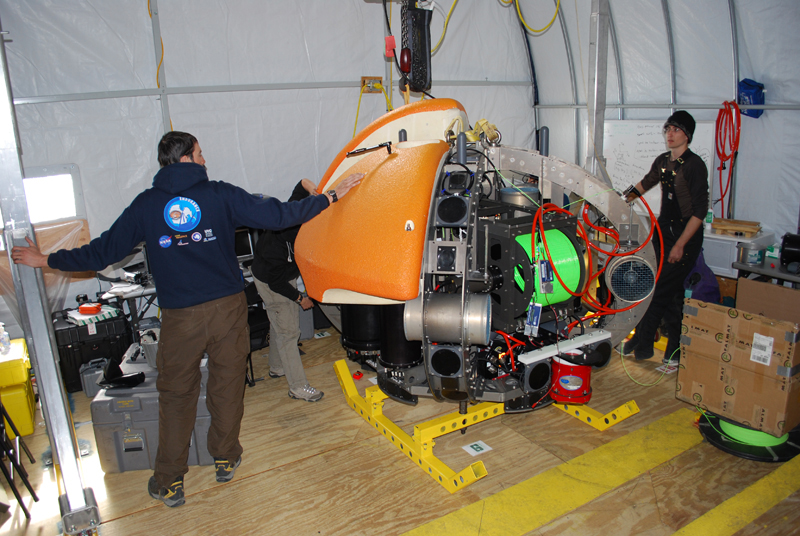
We put the orange syntactic blocks onto the vehicle to provide flotation
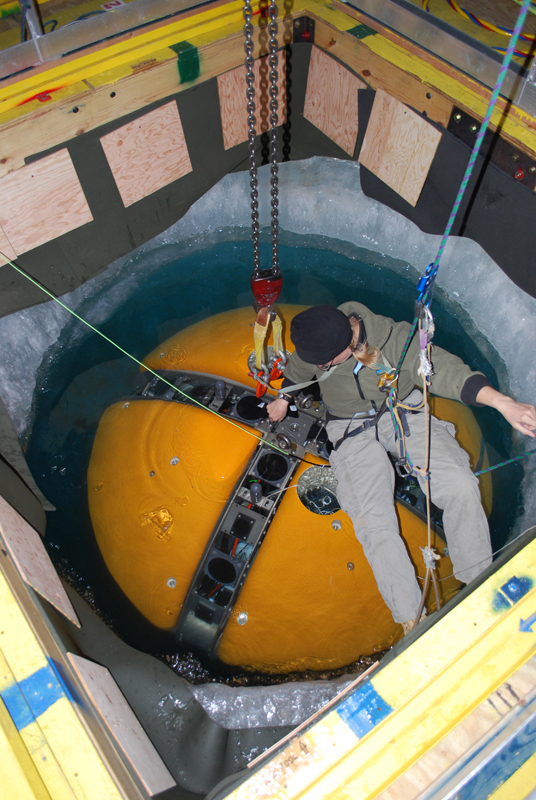
Vickie gets on rope to ballast the vehicle and get the buoyancy just right
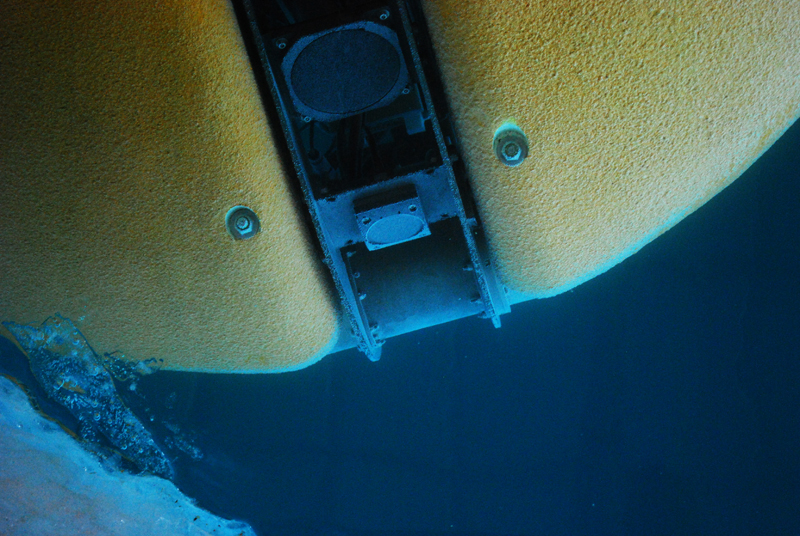
The white speckles and fuzz on the bot in this photo are actually thousands of tiny, trouble-making microbubbles.
Friday
December 5, 2008
The first people bringing their breakfasts into our camp
mess
tent this morning found Bart already on the phone with the servo driver
manufacturer. Fortunately, when the comm techs set us up for
internet, they also gave us a VOIP phone. After breakfast we tore
ourselves away from eavesdropping on Bart’s conversation with tech
support to start work out in the Bot House. Just because the
profiler is temporarily stalled doesn’t mean we can’t proceed with
other tests, so the plan of the day was to put the bot in the water
with the syntactic on and take it for its first Antarctic swim.
Before taking the bot down under the ice, we wanted to make sure that
the bottom perimeter of the ice hole was snag free. The lake ice
is about 3 meters thick and the level of the lake water in the melt
hole is about 30 centimeters below the ice surface. The other 2.7
meters of the hole is underwater and this makes it difficult for us to
judge if the wall surface is smooth or jagged. To give us a
definitive answer, Peter decided to do an ice dive and have a
look. As he donned all of the gear associated with ice diving in
Antarctica — layers of fleece, a drysuit, dry gloves, and a full face
mask — Vickie hooked up his air supply. In these kinds of ice
dives, it is nice to keep the scuba tanks in the warm air at the
surface and run long hoses from the tanks to the diver’s full face
mask. This keeps the tanks and first stage regulators warm,
making the dive safer and more enjoyable. The full face mask
includes a comm unit so we could talk to Peter during his dive.
He took an ice chipper bar down and busted off all of the jagged
corners at the bottom of the ice hole.
Once the melt hole was prepared it was time to get the bot ready to
swim. We put the syntactic blocks on, lifted the vehicle with the
hoist and set it in the water. To make the bot as power-efficient
as possible, we always ballast and trim the vehicle. To ballast,
we add or remove lead weights to the bot to make it neutrally buoyant,
so that without hooks attached it floats just under the surface of the
water and neither sinks nor rises. To trim the bot we place the
lead weights we’re using for ballast in specific locations on the bot’s
frame so that it sits level in the water. The whole process is a
little time consuming but a neutrally buoyant and well-trimmed bot
won’t use much battery power for thrusting, so it is important to get
it just right. In our previous tests in tanks or at the quarry in
Austin, it was easy to add and remove lead because you could just lean
over the vehicle. Here, however, there is about a meter drop from
the top of the platform to the water level, where the vehicle is
floating and you would have to lean out horizontally as well, to work
with the ballast. Since we didn’t want to drop either a person or
our lead weights into the icy water, Vickie rigged a climbing rope to
the gantry and, wearing a harness and using climbing ascenders, hung
just above the robot to adjust the lead weights more easily.
Once we felt confident that the vehicle was ballasted properly,
Kristof, Shilpa and Chris took their seats at the mission control table
and drove the vehicle down and under the ice for the first time.
“The ice is smooth!” Shilpa reported.
This was a relief. The top surface of the lake ice is anything
but smooth: it is scalloped and cracked with plateaus and valleys
and in places can vary in height by half a meter. So naturally we
wondered about the underside of the ice. We hoped it would be
smooth because it would make navigation easier and it would be less
likely for our fiber optic line to become ensnared. We all
crowded around the monitor displaying the view of the horizontal-facing
camera. Yes, the ice was smooth as glass.
We motored the bot around under the ice testing the various sensors in
action. After a while we noticed that some of the sensors that
use sonar elements started to drop out and we didn’t know why. We
brought the vehicle back to the surface to check it out. As the
bot rose up through the hole we noticed that it looked different, kind
of…fuzzy. Also, it was too buoyant. At the end of its
ascent, the bot was riding almost 2 inches higher in the water than it
had when we ballasted it half an hour before. Looking closer we
learned that the white “fuzz” we were seeing on the bot was actually
thousands and thousands of tiny bubbles coating the entire exterior of
the vehicle.
The lake water is supersaturated in dissolved gases and as the bot
moved through the water, some of this gas was apparently coming out of
solution and forming these microbubbles on the robot’s surfaces.
The microbubbles were making the bot significantly more buoyant and
were interfering with the acoustics of the sonar transducers.
We’ve never had the bot in such gas-rich waters before and didn’t
predict this kind of problem.
While we found this surprise to be another puzzle we have to deal with,
Peter reminded us all that this is the kind of stuff we are here to
learn about. There are two parts to the Endurance mission here in
Antarctica: one is to collect data from Lake Bonney and the other is to
develop some of the technology that an AUV on Europa would use.
In this way, our field work here is proving to be a good analog for a
mission on Europa. The exploration of Europa is bound contain
some surprises, just like our exploration of Lake Bonney and the
microbubbles. The more we can learn about possible issues like
these in the experimental phase here on Earth, the better we could
design an AUV for alien environments.
Our attempt at a quick fix for the microbubbles on the sonars was to
take a small amount of Simple Green hand cleaner and rub it over the
sonar faces. This seems to keep the bubbles from forming on these
surfaces but we might be able to find a better substance to act as a
surfactant here. To counter the extra lift given by the bubbles,
for now we just threw an extra pound of lead on the vehicle.
We took the bot back down under the ice for some more tests. For
one thing we wanted to test one of our bot recovery procedures.
Now that we knew that the underside of the ice was smooth, we figured
that if the bot were to die, that is, lose communications with mission
control run out of battery power, we could pull it back in by hand by
tugging on the fiber optic line we use to communicate with the bot’s
cPCI. To make sure, we did a practice run of physically pulling
the bot back in with an extra safety cord we had tied on. It
worked very easily, so we know that in a crisis we have a way to get
the bot back.
During this emergency practice, we had the upward-looking camera on,
and were displaying its images on one of the mission control
monitors. The upward-looking cam is at the top of the bot and
faces directly up. Normally we would only use it for visual
homing to help the bot return to the melt hole at the end of a
mission. What we didn’t expect is the kind of images we would see
while the bot was just running around under the ice. We found
that the ice was amazingly clear and that a lot of sunlight came
through. There are thousands of bubbles in the ice. Some
bubbles contain sediment that was blown onto the ice from the land and
frozen in, some bubbles are white and clear. They form columns
going from the bottom towards the top. It was beautiful and Peter
added enthusiastically that the views from this upward camera were a
source of data that no one had recognized before. The ice was
clear enough that we could even tell when we had crossed under the Bot
House floor.
When we finished the remaining tests for the day we pulled the bot up
for the night, put the batteries on charge and went back for dinner.
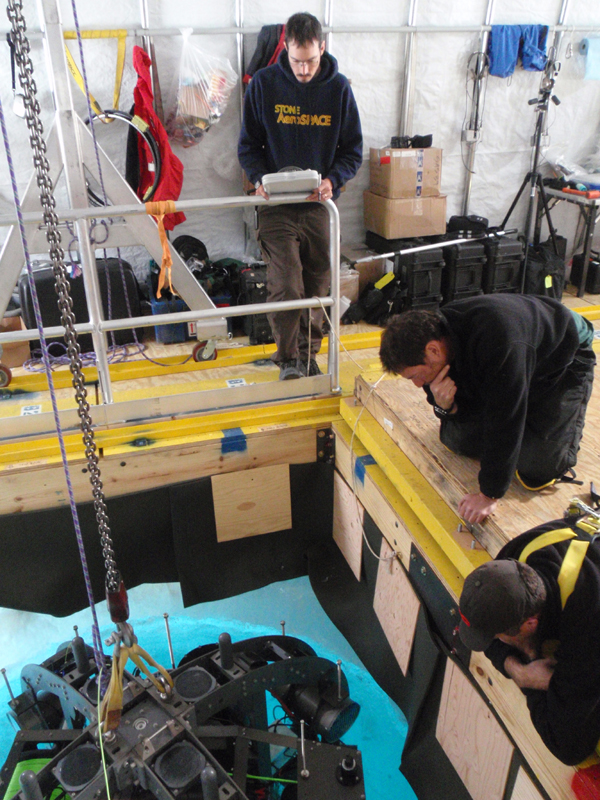
Kristof, John, and Peter watch intently as the bot is lowered into the melt hole for the first time
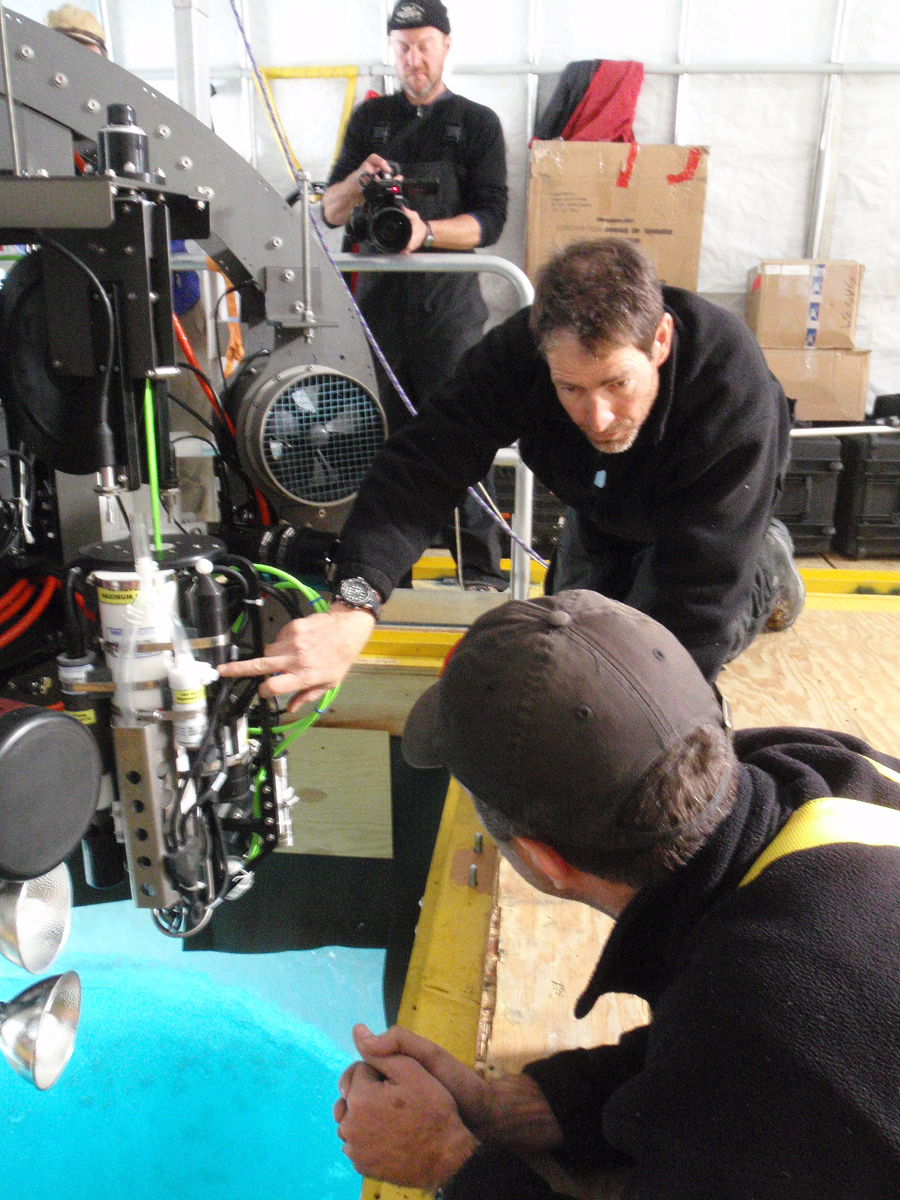
John and Peter get the Seabird pump on the drop sonde working
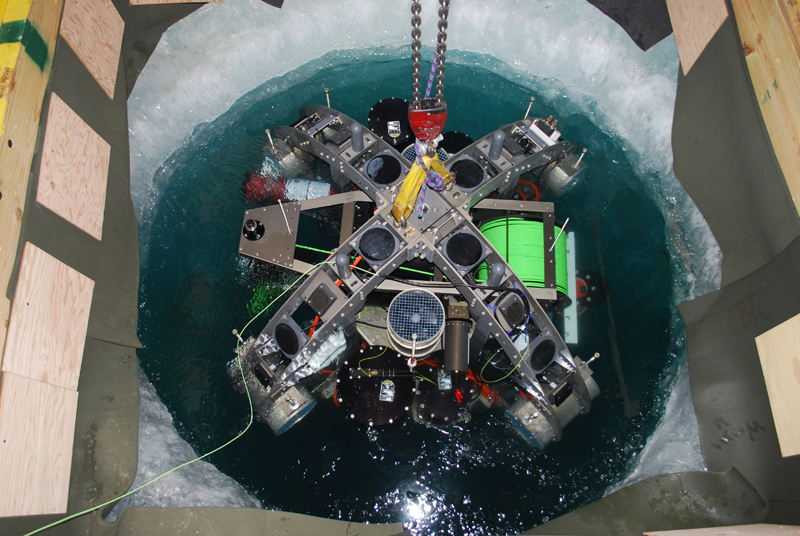
We watch from above as the spooler drum (on the right) unwinds the bright green Ethernet cable that holds the sonde (underwater on the far left)
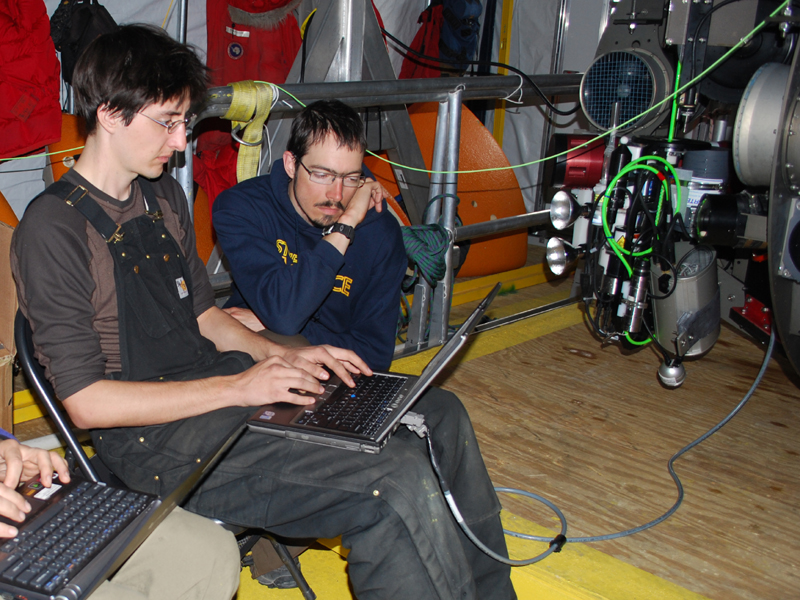
With the bot back on the surface, Chris plugs directly into the profiler electronics pod to investigate the servo motor malfunction while Kristof looks on
Thursday
December 4, 2008
Today we put the bot in the water. Since the
vehicle hasn’t been wet since our last tests at NBL (NASA’s Neutral
Buoyancy Lab) in August we wanted to check all of the electronics pods
for leaks and check that all of sensors and instruments were
working. The bot has traveled halfway around the world, after
all. To do these checks we hung the bot from the hoist without
the orange syntactic blocks we normally use to make the vehicle
float. John and Peter paid particular attention to their
scientific instruments on the drop sonde. They adjusted the water
pump on the sonde, raising the bot out, priming the pump and lowering
it again a few times to watch its behavior. With the pump in
order, Chris, Shilpa and Kristof ran through the checklist of sensors
and electronics: No pod leaks, Sonars working, DVL (Doppler
Velocity Log), depth sensors, IMU (Inertial Measurement Unit), cameras,
lights and so on, all working. Check, check, check…
One of the last few tests was to check the science payload package, the
profiler. The profiler is made up of several parts. First
there is the drop sonde, basically an aluminum frame with all Peter and
John's water chemistry instruments strapped onto it. This sonde
hangs from the bot by a Kevlar reinforced Ethernet cable. The
cable feeds over a pulley and onto a large spool on the opposite side
of the vehicle. Servo motors spin the spool to raise and lower
the sonde through the different water strata in the lake.
Normally, with the floatation blocks in place, we are not able to see
much of the spooler functioning, only the up and down motion of the
sonde is visible. Since we left blocks off for this test were
able to watch the entire profiler in action underwater. It was
satisfying to see how smoothly the level winder guided the green
Ethernet cable between the spool and the pulley as it wound and
unwound, raising and lowering the sonde. Several minutes into the
test run, however, the spooler stopped unexpectedly. Chris noted
that the software was reporting a temperature fault—it was too
cold. What we found was that if we heated the electronics pod for
the profiler in air with the Herman Nelson heater, the driver would
function correctly but once the pod had cooled to 10ºC in the
nearly freezing water, the driver would stop.
Of course we had considered the effects of Antarctic temperatures on
the vehicle before. We wondered if such cold water would cause
equipment malfunctions. In February we operated the bot under ice
in Lake Mendota in Madison, Wisconsin. Those tests identified a
problem with the electronics that control the thrusters. We later
traced that problem back to some poorly soldered connections—a slip in
quality control from the manufacturer. The faulty electronics
were immediately replaced and the bot suffered no further problems from
the cold. But during the February tests in Wisconsin the profiler
was still in the design phase, it didn’t exist and thus couldn’t be
cold tested. So what exactly is the problem? Is there a way
we can fix it in the software settings, a minimum temperature parameter
we can change to allow the servos to run at lower temperature?
There isn’t anything about it in the servos’ manual and, given the time
difference between here and the states, we’ll have to wait until
morning to ask the manufacturer.
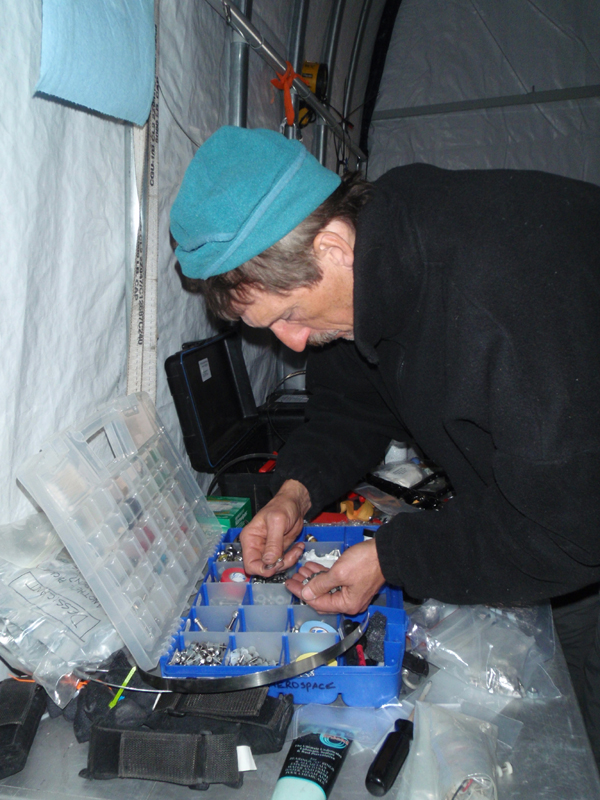
Bill finds some hardware to use on a new mounting bracket for the DeltaT sonar
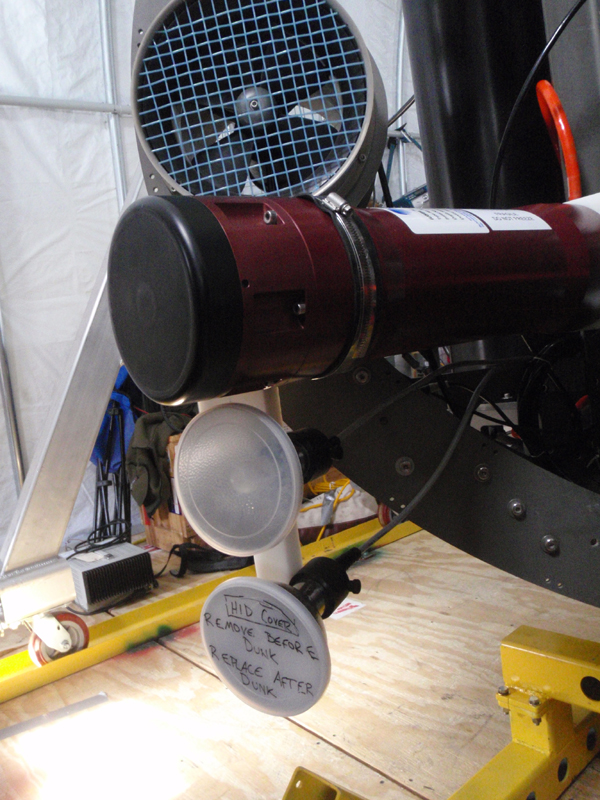
The USBL and HID lights were just a few of the components to attached to the bot today
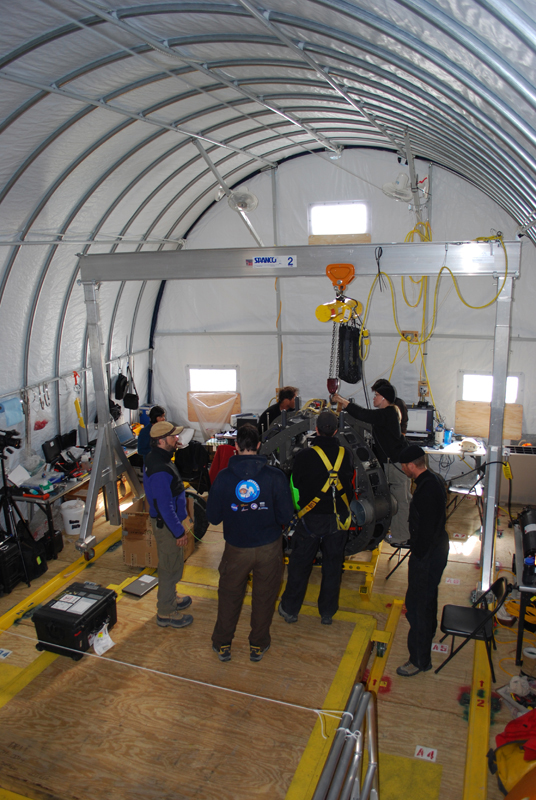
The team works to get the bot put back together and get the Bot House set up as a workshop / mission control
Wednesday
December 3, 2008
After our brief stint as Antarctic carpenters, we
have returned
to doing what we do best — working with the robot. Today we got the
Bot House set up as a working mission control. The programmers
set up their computers along the far wall and boxes of tools, robot
batteries and spare parts were unpacked and set up on tables along the
two long walls of the building. The bot and gantry dominate our
workspace and setting up desk and bench space for 8 programmers and
technicians was a little tricky. With everything unpacked and the
empty shipping cases stacked high along the walls we set about getting
the bot into working order.
First of all, the bot had to be put back together. In Texas,
before we shipped the bot to the Ice, we removed the most delicate
sensors and packed them in padded cases to be shipped separately.
This ensured that they weren’t damaged in transport and it reduced the
weight of the remaining vehicle so that it would be light enough to be
flown on the helo trip from McMurdo to Lake Bonney. Now that
we’re here though, all of these sensors had to go back on before we can
think about putting the bot in the water.
As Vickie bolted each sensor back to its proper place, Shilpa and
Kristof worked on some of the vehicle code. Chris and Bob
assessed the bot’s giant batteries and started charging them up. Bart
sorted hardware and worked on developing mission plans. When
Vickie went to mount the Delta T sonar to the vehicle she noticed that
the bracket that should attach the instrument to the bot wasn’t
here. Talking with Bill, they realized that somehow in the rush
and confusion of packing the vehicle, tools, spare parts and whatnot in
Texas, the bracket they had ordered had never been delivered and thus
never brought. Bill and Peter therefore, designed and constructed
a new mounting bracket out of some extra prototyping materials we had
brought along for just this kind of thing. So far this looks like
the only thing that didn’t make it to Antarctica from Texas, not bad!
At the end of the day, most of the vehicle is back together and we
should be able to start real testing tomorrow.
Blog entries from previous weeks
can be found below:
Week 1 - Nov 26, 2008 - December 2, 2008